①The basic way of printing
Printing according to printing equipment can be divided into direct printing, discharge printing and anti-dyeing printing.
1.Direct printing Direct printing is a kind of printing directly on white fabric or on fabric that has been pre-dyed. The latter is called a mask print. Of course, the color of the print pattern is much darker than the background color. A large number of common printing methods are direct printing. If the background color of the fabric is white or mostly white, and the print pattern looks lighter from the back than the front color, then we can determine that this is a direct printed fabric (note: due to the strong penetration of the printing paste, so the light fabric can not be judged by this method). If the front and back of the fabric background color are the same (because it is a piece dye), and the print pattern is much darker than the background color, then this is the cover print fabric.
2. Discharge printing Discharge printing is carried out in two steps, the first step is to dye the fabric monochrome, and the second step is to print the pattern on the fabric. The printing paste in the second step contains a strong bleaching agent that can destroy the base color dye, so this method can produce blue and white polka dot patterning cloth, which is called white extraction.
When the bleach and the dye that will not react with it are mixed in the same color paste (VAT dyes belong to this type), color extraction printing can be carried out. Therefore, when a suitable yellow dye (such as VAT dye) is mixed with a colored bleach, a yellow polka dot pattern can be printed on a blue-bottom fabric.
Because the base color of discharge printing is first dyed by the piece dyeing method, if the same base color is printed on the ground than the color is much richer and deeper. This is the main purpose of discharge printing. Discharge printing fabrics can be printed by roller printing and screen printing, but not by heat transfer printing. Because of the high production cost of the printed fabric compared with direct printing, the use of the required reducing agent must be carefully and accurately controlled. Fabrics printed in this way have better sales and higher price grades. Sometimes, the reducing agents used in this process can cause damage or destruction of the fabric in the printed pattern. If the color of both sides of the fabric is the same (because it is a piece dye), and the pattern is white or a different color from the background color, it can be confirmed that it is discharge printed fabric.
3. Anti-dye printing Anti-dye printing includes two stages:
(1) The white fabric is printed with chemicals or waxy resins that prevent or prevent the dye from penetrating into the fabric;
(2) piece dyed fabric. The purpose is to dye the base color to bring out the white pattern. Note that the result is the same as that of discharge printed fabric, however the method used to achieve this result is the opposite of discharge printed fabric. The application of anti-dye printing method is not common, and it is generally used when the base color cannot be discharged. Rather than a large-scale production basis, most anti-dye printing is achieved through methods such as handicraft or hand printing (such as wax anti-printing). Because discharge printing and anti-dye printing produce the same printing effect, it is usually not distinguishable by naked eye observation.
4. Paint printing The use of paint rather than dye to produce printed fabrics has become so widespread that it has begun to be regarded as an independent printing method. Paint printing is the direct printing of paint, the process is often called dry printing, in order to distinguish from wet printing (or dye printing). By comparing the hardness difference between the printed part and the unprinted part on the same fabric, the paint printing and the dye printing can be distinguished. The paint printed area feels a little harder than the unprinted area, perhaps a little thicker. If the fabric is printed with dye, there is no significant difference in hardness between the printed part and the unprinted part.
Dark paint prints are likely to feel harder and less flexible than light or light colors. When examining a piece of fabric with paint prints present, be sure to check all colors, as both dye and paint may be present on the same piece of fabric. White paint is also used for printing, and this factor should not be overlooked. Paint printing is the cheapest printing method in printing production, because the printing of paint is relatively simple, the required process is minimal, and usually does not require steaming and washing.
Coatings come in bright, rich colors and can be used on all textile fibers. Their light fastness and dry cleaning fastness are good, even excellent, so they are widely used in decorative fabrics, curtain fabrics and clothing fabrics that need dry cleaning. In addition, the coating almost does not produce large color differences on different batches of fabric, and the coverage of the base color is also very good when the mask is printed.
Special printing
The basic way of printing (as mentioned above) is to print a pattern on the fabric, each color in the pattern used in the printing and dyeing method, special printing belongs to the second category, the reason for this classification, because this method can obtain a special printing effect, or because the process cost is high and not widely used.
1. Floor printing Floor printing base color is obtained by printing method rather than using piece dyeing method. Usually in the printing process, both the base color and the color of the pattern are printed on the white cloth. Sometimes a full floor print is designed to mimic the effect of discharge or anti-dye prints that are more expensive to produce, but it is easy to distinguish different prints from the back of the fabric. The reverse side of the ground printing is lighter; Because the fabric is dyed first, both sides of the discharge or anti-dye printing are the same color.
The problem with full-floor printing is that sometimes large areas of background color cannot be covered by dark colors. When this problem occurs, carefully check the pattern on the ground, you will find some dim spots. This phenomenon is basically caused by washing, not due to the amount of dye covering.
These phenomena do not occur in high-quality printed fabrics produced under strict technological conditions. This phenomenon is not possible when the screen printing method is used to print all over the floor, because the color paste is scraped on, rather than rolled in like a roller printing. Floor-covered printed fabrics usually feel hard.
2. Flocking printing Flocking printing is the printing method in which the fiber pile called the fiber short pile (about 1/10-1/4 inch) is adhered to the surface of the fabric in a specific pattern. The two-stage process begins by printing a pattern on the fabric with an adhesive instead of a dye or paint, and then combines the fabric with a fiber stub, which stays in place only where the adhesive has been applied. There are two ways to attach short flocking to the fabric surface: mechanical flocking and electrostatic flocking. In mechanical flocking, short fibers are sifted onto the fabric as it passes through the flocking chamber in a flat width.
When stirred by the machine, the fabric vibrates, and the short fibers are randomly inserted into the fabric. In electrostatic flocking, static electricity is applied to the short fibers, resulting in an upright orientation of almost all fibers when glued to the fabric. Compared with mechanical flocking, electrostatic flocking is slower and more expensive, but it can produce a more uniform and dense flocking effect. The fibers used in electrostatic flocking include all fibers used in actual production, of which viscose fibers and nylon are the most common.
In most cases, staple fibers are dyed before being transplanted into the fabric. The ability of the flocking fabric to withstand dry cleaning and/or washing depends on the nature of the adhesive. Many high-quality adhesives used in fabric processing have excellent fastness to washing, dry cleaning, or both. Because not all adhesives can withstand any type of cleaning, it is necessary to verify which cleaning method is suitable for any particular flocking fabric.
3.Warp printing Warp printing means that before weaving, the warp of the fabric is printed and then woven together with the plain weft (usually white) to create the fabric, but sometimes the color of the weft is very different from the color of the printed warp. The result is a soft shadow-grain, even blurred pattern effect on the fabric. The production of warp printing requires care and detail, so it is almost only found on high-grade fabrics, but fabrics made with fibers that can be printed by heat transfer are an exception. With the development of warp heat transfer printing, the cost of warp printing has been greatly reduced. Warp printing can be identified by pulling out the warp and weft of the fabric, because only the warp has the color of the pattern, and the weft is white or plain. Imitation warp printing effects can also be printed, but this is easy to identify because the color of the pattern is present on both the warp and weft.
4.burnt out printing
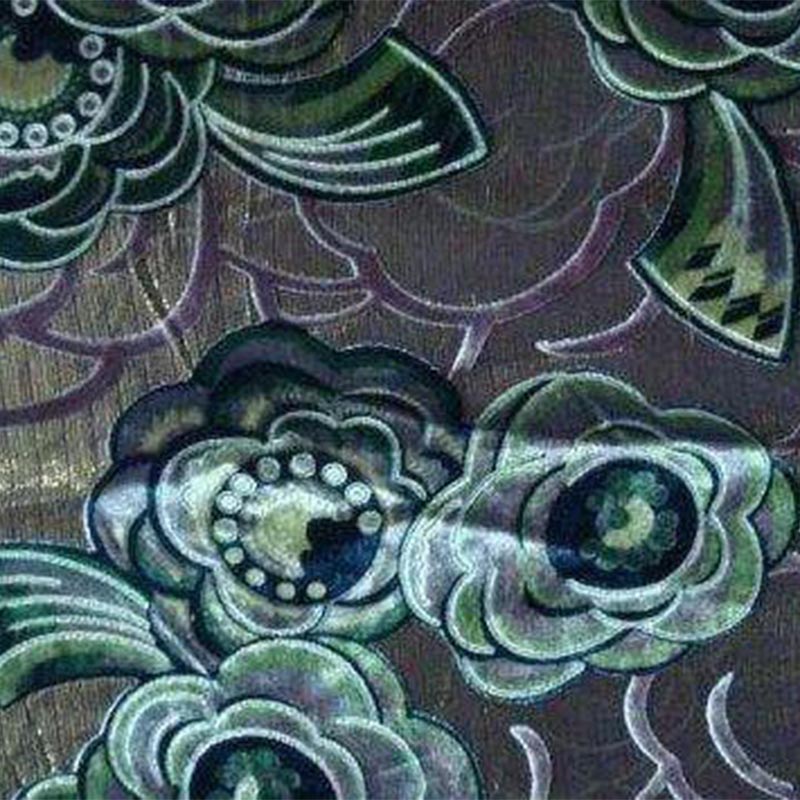
Rot printing is the printing of chemicals that can damage fiber tissue on the pattern. As a result, there are holes where the chemicals come into contact with the fabric. Imitation mesh embroidery fabric can be obtained by printing with 2 or 3 rollers, one roller contains destructive chemicals, and the other rollers print the stitch of imitation embroidery.
These fabrics are used for cheap summer blouses and raw edges for cotton lingerie. The edges of holes in worn prints are always subjected to premature wear, so the fabric has poor durability. Another type of floral print is fabrics made of blended yarn, core-coated yarn, or a mixture of two or more fibers, where chemicals can destroy one fiber (cellulose), leaving the others undamaged. This printing method can print many special and interesting printed fabrics.
The fabric can be made of viscose/polyester 50/50 blended yarn, and when printing, the viscose fiber part disappears (rotted away), leaving the undamaged polyester fiber, resulting in the printing of only polyester yarn, and the unprinted polyester/viscose fiber blended yarn original sample.
5.Double-sided printing
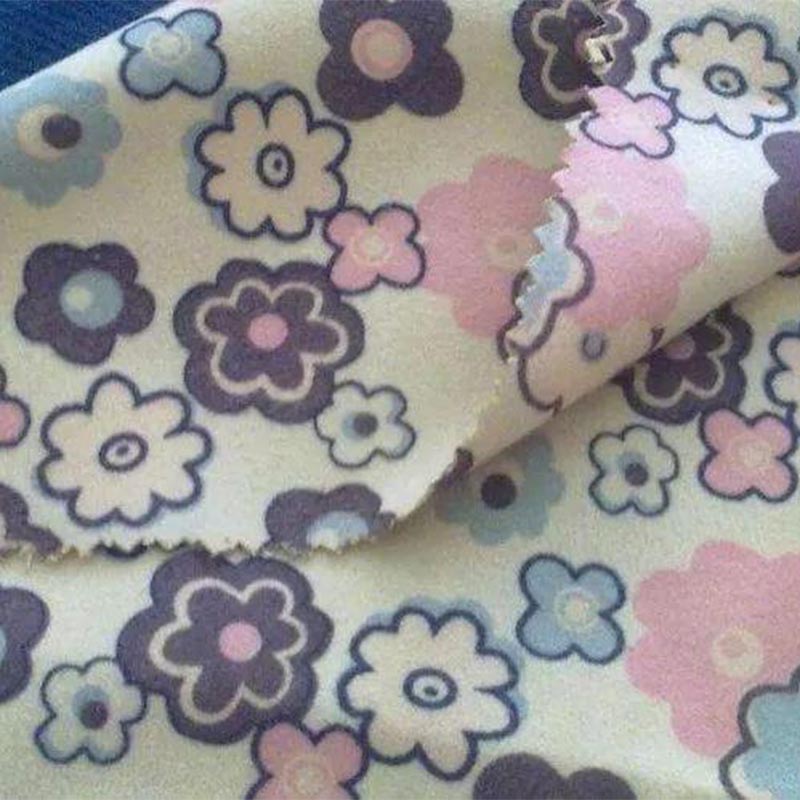
Double-sided printing is printing on both sides of the fabric to obtain a double-sided effect of the fabric, similar to the appearance of packaging fabrics printed with a coordinated pattern on both sides. The end use is limited to double-sided sheets, tablecloths, lineless or double-sided jackets and shirts.
6. Special prints Special prints are prints with two or more unique patterns, each printed on a different area of the fabric, so each pattern will be located in a specific position in the garment. For example, a fashion designer would design a blouse with blue and white polka dots on the front and back, with the same blue and white sleeves, but with a striped pattern. In this case, the clothing designer works with the fabric designer to create both polka dot and stripe elements on the same roll. The layout of the printing position and the number of fabric yards required for each pattern element must be carefully arranged so that the fabric utilization rate is optimal and does not cause too much waste. Another kind of special printing is printed on already cut pieces of clothing, such as bags and collars, so that many different and unique clothing patterns can be created. Sheets can be printed by hand or by heat transfer.
The traditional printing process includes pattern design, cylinder engraving (or screen plate making, round screen production), color paste modulation and printed pattern, post-treatment (steaming, desizing, washing) and other four processes.
②pattern design
1.According to the use of the fabric (such as men's, women's, ties, scarves, etc.) grasp the style, tone and pattern of the pattern.
2. In harmony with the style of fabric material, such as silk and hemp products exquisite degree and color purity have very big difference.
3. The expression techniques of the pattern, the structure of the color and the pattern should cater to the printing process and the width of the fabric, the direction of the thread, the cutting and sewing of the clothing and other factors. Especially the different printing methods, the pattern style and performance techniques are also different, such as the number of color sets of roller printing is 1 to 6 sets, and the flower width is limited by the size of the roller; The number of color sets of screen printing can reach more than 10 sets, and the arrangement cycle can be large enough to print a single fabric, but it is not suitable for the design of neat and regular geometric patterns.
4. Pattern style design should consider market and economic benefits
③Flower cylinder carving, screen plate making, round net making
The cylinder, screen and round screen are the specific equipment of the printing process. In order to make the designed pattern produce the corresponding pattern on the fabric under the action of the color paste, it is necessary to carry out the process engineering such as cylinder engraving, screen plate making and circular net making, so as to form the corresponding pattern model.
1. Cylinder engraving: cylinder printing machine printing, pattern engraving on the copper cylinder, there are twill lines or dots, used to store color paste. The process of carving concave patterns on the surface of the copper roller is called cylinder engraving. The cylinder is made of iron hollow roll copper plated or cast with copper, the circumference is generally 400 ~ 500mm, the length depends on the amplitude of the printing machine. Pattern engraving methods include hand engraving, copper core engraving, small engraving, photographic engraving, electronic engraving and so on.
2. Screen plate making: flat screen printing needs to make the corresponding screen. Flat screen plate making includes screen frame making, mesh making and screen pattern making. The screen frame is made of hard wood or aluminum alloy material, and then a certain specification of nylon, polyester or silk fabric is stretched on the screen frame, that is, the screen. The production of screen patterns is commonly used by photosensitive method (or electronic color separation method) or anti-paint method.
3. Round net production: Round net printing needs to be made. A nickel net with holes is first made, and then a round metal frame is set at both ends of the nickel net to tighten the nickel net. Then the nickel net is coated with photosensitive glue, the pattern of color separation sample is tightly wrapped in the nickel net, and the circular net with pattern is formed by photosensitive method.
4.Color paste modulation and printed pattern IV. Post-treatment (steaming, desizing, washing)
After printing and drying, it is usually necessary to carry out steaming, color development or solid color treatment, and then carry out desizing and washing to fully remove the paste, chemical agents and floating color in the color paste.
Steaming is also called steaming. After the printing paste is dried on the fabric, in order to transfer the dye from the paste to the fiber and complete certain chemical changes, it is generally necessary to steam. In the steaming process, the steam first condenses on the fabric, the fabric temperature rises, the fiber and the paste swell, the dye and chemical agents dissolve, and some chemical reactions occur, at this time the dye is transferred from the paste to the fiber, thus completing the dyeing process.
In addition, due to the presence of paste, the dyeing process of printing dyes is more complicated, and the evaporation time is longer than that of pad dyeing. Steaming conditions also vary with the properties of dyes and fabrics.
Finally, the printed fabric should be fully desized and washed to remove the paste, chemical reagents and floating color on the fabric. The paste remains on the fabric, making it feel rough. The floating color remains on the fabric, which will affect the color brightness and dyeing fastness.
A flaw in the printed fabric
The most common printing defects caused by the printing process are listed and described below. These defects may be caused by improper handling in the printing process, improper handling of the fabric before printing, or defects in the printed material itself. Because textile printing is similar to dyeing in many ways, many of the defects that occur in dyeing are also present in printed fabrics.
1.Printing drag printing paste stain due to friction before drying.
2.Color printing paste splashing down on fabric is not smooth, but spilt on or splashed on the fabric, color point or splashing color.
3.The pattern of fuzzy edge is not smooth, the line is not clear, most often caused by improper singeing or paste concentration is not appropriate.
4.The flowers are not allowed to be due to the printing roller or screen vertically aligned, cause pattern before and after the registration is not accurate. This defect is also called mismatching or pattern shifting.
5.Stop printing because of printing machine in the printing process stopped suddenly, and then switched on, the results produced in the fabric color.
6. Part of the embrittlement on the printed fabric, printed with one or more color place often is damaged, usually due to damaging chemicals used in printing paste. This problem can also be found in the drawing part of the discharge printed fabric.
Post time: Mar-11-2025